WOOL
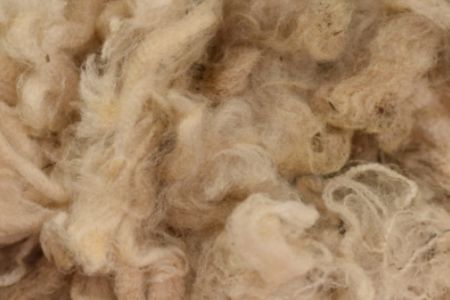
We understand that to make fine quality fabrics, we need to source best quality wool. Clean or scoured wool is delivered to our mill by reliable suppliers from around the world. Before the wool is delivered to our compound scouring is done to remove impurities such as dirt, grease and suint.